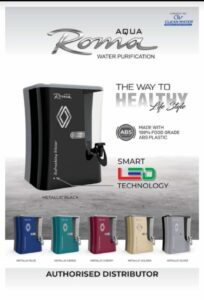
Here are key features and aspects related to domestic reverse osmosis:
Filtration Process: In a domestic reverse osmosis system, water from the tap is forced through a specialized membrane that allows only water molecules to pass through while blocking contaminants such as minerals, heavy metals, bacteria, viruses, and other impurities. The membrane acts as a barrier, producing purified water on one side and directing impurities to another.
Removal of Contaminants: Domestic reverse osmosis systems are effective in removing a wide range of contaminants, including chlorine, sediment, arsenic, fluoride, nitrates, and more. The result is clean and purified water that is often free from odors, tastes, and visible particles.
Point–of–Use Application: These systems are designed for point-of-use application, typically installed under the kitchen sink. They may consist of multiple stages of filtration, including pre-filters, the reverse osmosis membrane, and post-filters to further enhance water quality.
Compact Design: Domestic reverse osmosis systems are generally compact and designed for easy installation. They are suitable for residential spaces where space may be limited.
Improved Taste and Quality: By removing impurities, a domestic RO system can significantly improve the taste, odor, and overall quality of tap water, providing a reliable source of clean drinking water within the home.
Maintenance Requirements: Regular maintenance is essential for optimal performance. This may include replacing pre-filters, post-filters, and the RO membrane at recommended intervals to ensure efficient contaminant removal.
Waste Water Generation: One consideration with domestic reverse osmosis is the generation of wastewater, as not all water passing through the system becomes purified. Some systems incorporate mechanisms to minimize waste, such as by utilizing permeate pumps or water-saving technologies.
Cost Considerations: Domestic reverse osmosis systems vary in cost, and factors such as the complexity of the system, the number of filtration stages, and brand reputation can influence the price. While there is an initial investment, many homeowners find the improved water quality to be a valuable and worthwhile benefit.
Before installing a domestic reverse osmosis system, it’s essential to assess the water quality, understand local regulations, and consider the specific needs of the household to select an appropriate system. Regular maintenance and adherence to manufacturer guidelines are crucial for the continued effectiveness of the system.
INDUSTRIAL REVERSE OSMOSIS (RO)
Industrial reverse osmosis is a water purification process commonly employed in various industries to treat and purify large volumes of water for different applications. The industrial scale of reverse osmosis allows for the removal of contaminants, dissolved solids, and impurities, making it suitable for applications such as boiler feedwater, pharmaceutical production, food and beverage processing, electronics manufacturing, and more. Here are key features and aspects related to industrial reverse osmosis:
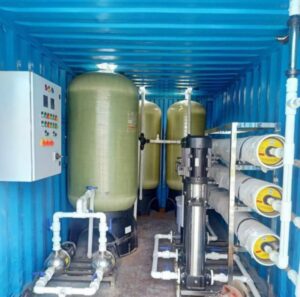
High Capacity: Industrial reverse osmosis systems are designed to handle
large volumes of water, ranging from hundreds to thousands of gallons per day.
The high capacity makes them suitable for industrial processes that require a
significant amount of purified water.
Multi–Stage Filtration: Industrial RO systems typically consist of multiple
stages of filtration. These stages may include pre-filters to remove larger
particles, carbon filters to remove chlorine and organic matter, and the
reverse osmosis membrane for fine filtration and separation of dissolved
solids.
Customization: Industrial reverse osmosis systems can be customized to
meet the specific water quality requirements of different industries. The
configuration of the system, the type of membrane used, and additional
treatment stages can be tailored to address the unique challenges of the water
source and the intended application.
Efficient Contaminant Removal: The reverse osmosis process is
highly effective in removing a wide range of contaminants, including salts,
minerals, heavy metals, bacteria, viruses, and organic compounds. This ensures
that the treated water meets stringent quality standards required for
industrial processes.
Water Reuse and Recycling :
In many industrial settings, there is an increasing emphasis on water reuse and
recycling to enhance sustainability. Industrial reverse osmosis systems play a
crucial role in treating wastewater and making it suitable for reuse in
processes, thus reducing overall water consumption.
Prevention of Scaling and Fouling: Industrial RO systems often
incorporate anti-scaling and anti-fouling measures to prevent the build-up of
mineral deposits on the membrane surface. This helps maintain the efficiency of
the system and prolong the life of the membrane.
Continuous Monitoring and Automation: Industrial reverse osmosis systems
are equipped with monitoring and control systems that ensure the proper
functioning of the system. Automation allows for real-time adjustments to
optimize performance and respond to changes in water quality.
Compliance with Industry Standards: Industrial reverse osmosis systems
are designed to meet or exceed industry standards and regulatory requirements
for water quality. Compliance with these standards is crucial, especially in
industries such as pharmaceuticals and electronics manufacturing where water
quality is a critical factor.
Energy Efficiency: Advanced industrial RO systems may incorporate energy
recovery devices and other technologies to improve energy efficiency, reducing
operational costs and environmental impact.
Regular Maintenance: Like their domestic counterparts, industrial reverse
osmosis systems require regular maintenance to ensure optimal performance. This
includes monitoring membrane condition, replacing filters, and addressing any
issues promptly.
Industrial
reverse osmosis systems are essential for various industries where water
quality is a critical factor in manufacturing processes. They provide a
reliable and efficient means of producing high-quality water at a large scale,
contributing to both operational efficiency and environmental sustainability.
SEAWAGE TREATMENT PLANT
A sewage treatment plant is a facility designed to treat and process wastewater from residential, commercial, and industrial sources. Its primary goal is to remove contaminants and pollutants from the sewage to produce treated water that can be safely discharged into the environment or reused for non-potable purposes. Here are key components and processes commonly found in a sewage treatment plant.
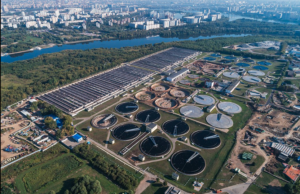
Screening:
The incoming sewage is first screened to remove large objects such as sticks, leaves, plastic, and other debris. This helps prevent damage to pumps and equipment in subsequent treatment stages.
Primary Treatment:
In this stage, the sewage flows into primary settling tanks, where heavy solids settle to the bottom as sludge, and lighter materials, like grease and oil, float to the surface. The separated sludge is typically pumped to sludge treatment processes, while the clarified liquid undergoes further treatment.
Biological Treatment (Secondary Treatment):
The clarified liquid from the primary treatment is then subjected to biological treatment. This often involves using activated sludge or other biological processes where microorganisms break down organic matter present in the sewage, converting it into more stable forms. This stage helps reduce the concentration of organic pollutants.
Aeration Tanks:
Aeration tanks provide an environment with high oxygen levels to support the growth and activity of aerobic bacteria. These bacteria play a crucial role in breaking down organic pollutants through the process of oxidation.
Secondary Settling Tanks:
Following biological treatment, the water is directed to secondary settling tanks. Here, the remaining suspended solids formed during the biological treatment settle out as sludge, leaving clarified water that is ready for further treatment or discharge Tertiary.
Treatment (Advanced Treatment):
Depending on the regulatory requirements and the intended use of the treated water, a sewage treatment plant may include tertiary treatment processes. Tertiary treatment can involve additional filtration, chemical treatment, or advanced technologies to further reduce nutrient levels, pathogens, and trace contaminants.
Disinfection:
To ensure that the treated water is safe for release into the environment, disinfection is often employed. Common disinfection methods include chlorination, ultraviolet (UV) radiation, or ozonation. This step helps eliminate any remaining bacteria, viruses, or other harmful microorganisms.
Sludge Treatment:
The sludge collected during the primary and secondary treatment stages undergoes further treatment to reduce its volume and stabilize its composition. Common methods include anaerobic digestion, aerobic digestion, or mechanical dewatering. The treated sludge may be used for land application as fertilizer or sent to a landfill.
Effluent Discharge or Reuse:
The final treated water, known as effluent, can be discharged into receiving water bodies, such as rivers or oceans, if it meets regulatory standards.
EFFLUENT TREATMENT PLANT
An Effluent Treatment Plant (ETP) is a facility designed to treat industrial wastewater, often referred to as effluent, before it is discharged into the environment or municipal sewer systems. The primary objective of an ETP is to remove pollutants and contaminants from industrial effluents to ensure compliance with environmental regulations and protect natural water bodies. Here are key components and processes commonly found in an Effluent Treatment Plant
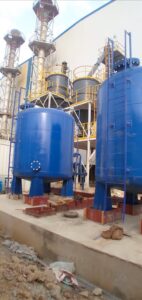
Similar to sewage treatment plants, the first step in many ETPs involves screening to remove large objects and debris from the industrial wastewater. This prevents damage to downstream equipment and facilitates smoother operation.
Equalization Tank:
Industrial effluents often vary in flow rates and composition. An equalization tank helps balance these variations, ensuring a more consistent and manageable flow into the treatment process.
Chemical Treatment (Primary Treatment):
In the primary treatment stage, chemicals may be added to the effluent to facilitate the precipitation or coagulation of suspended solids. This helps in the removal of heavy metals, oil, and grease from the wastewater.
Physical Treatment (Primary Settling Tank):
The effluent then moves to a primary settling tank where larger particles settle to the bottom as sludge. This allows for the separation of solid contaminants from the liquid portion of the effluent.
Biological Treatment (Secondary Treatment):
Many ETPs include a biological treatment stage where microorganisms, such as bacteria, break down organic pollutants present in the effluent. Common biological treatment methods include activated sludge processes, biological filters, or sequencing batch reactors.
Aeration Tanks:
Aeration tanks provide oxygen to support the growth and activity of aerobic bacteria, facilitating the decomposition of organic matter in the effluent.
Secondary Settling Tanks:
After biological treatment, the effluent undergoes a secondary settling process where remaining suspended solids settle out, and clarified water is separated for further treatment.
Tertiary Treatment (Advanced Treatment):
Depending on the specific requirements and quality standards, some ETPs may include tertiary treatment processes. Tertiary treatment can involve additional filtration, chemical treatment, or advanced technologies to further polish the effluent and meet stringent discharge or reuse standards.
Disinfection:
To ensure the treated effluent is free from harmful microorganisms, a disinfection step may be employed. Common disinfection methods include chlorination, ultraviolet (UV) radiation, or ozonation.
Sludge Management:
Sludge generated during the treatment process is often subjected to further treatment to reduce volume and stabilize its composition. This may include processes such as anaerobic digestion, dewatering, or drying. The treated sludge can be disposed of or utilized beneficially, depending on its characteristics.
Effluent Discharge or Reuse:
The final treated effluent, meeting regulatory standards, can be discharged into receiving water bodies or municipal sewer systems. Alternatively, it may be reused within the industrial facility for non-potable purposes like cooling water or process water.
Monitoring and Compliance:
Continuous monitoring and testing of effluent quality are crucial in ETPs to ensure compliance with environmental regulations. Regular analysis helps in adjusting treatment parameters and processes to maintain optimal performance.
Effluent Treatment Plants are essential for industries to manage and mitigate the environmental impact of their wastewater discharge. The design and operation of an ETP depend on factors such as the type of industry, the characteristics of the effluent, local regulations, and the desired quality of the treated water.
WATER SOFTNER PLANT
A water softener plant is a facility or system designed to remove hardness minerals, primarily calcium and magnesium ions, from water. Water hardness is a common issue in many areas, and it can lead to problems such as scale buildup in pipes and appliances, reduced soap effectiveness, and increased energy consumption in water heating systems. Water softener plants use various methods to exchange or remove these hardness ions and provide softened water. Here are key components and processes commonly found in a water softener plant.
Similar
to sewage treatment plants, the first step in many ETPs involves screening to
remove large objects and debris from the industrial wastewater. This prevents
damage to downstream equipment and facilitates smoother operation.
Equalization
Tank:
Industrial
effluents often vary in flow rates and composition. An equalization tank helps
balance these variations, ensuring a more consistent and manageable flow into
the treatment process.
Chemical
Treatment (Primary Treatment):
In
the primary treatment stage, chemicals may be added to the effluent to
facilitate the precipitation or coagulation of suspended solids. This helps in
the removal of heavy metals, oil, and grease from the wastewater.
Physical
Treatment (Primary Settling Tank):
The
effluent then moves to a primary settling tank where larger particles settle to
the bottom as sludge. This allows for the separation of solid contaminants from
the liquid portion of the effluent.
Biological
Treatment (Secondary Treatment):
Many
ETPs include a biological treatment stage where microorganisms, such as
bacteria, break down organic pollutants present in the effluent. Common
biological treatment methods include activated sludge processes, biological
filters, or sequencing batch reactors.
Aeration
Tanks:
Aeration
tanks provide oxygen to support the growth and activity of aerobic bacteria,
facilitating the decomposition of organic matter in the effluent.
Secondary Settling Tanks:
After
biological treatment, the effluent undergoes a secondary settling process where
remaining suspended solids settle out, and clarified water is separated for
further treatment.
Tertiary
Treatment (Advanced Treatment):
Depending
on the specific requirements and quality standards, some ETPs may include
tertiary treatment processes. Tertiary treatment can involve additional
filtration, chemical treatment, or advanced technologies to further polish the
effluent and meet stringent discharge or reuse standards.
Disinfection:
To
ensure the treated effluent is free from harmful microorganisms, a disinfection
step may be employed. Common disinfection methods include chlorination,
ultraviolet (UV) radiation, or ozonation.
Sludge Management:
Sludge
generated during the treatment process is often subjected to further treatment
to reduce volume and stabilize its composition. This may include processes such
as anaerobic digestion, dewatering, or drying. The treated sludge can be
disposed of or utilized beneficially, depending on its characteristics.
Effluent Discharge or Reuse:
The
final treated effluent, meeting regulatory standards, can be discharged into
receiving water bodies or municipal sewer systems. Alternatively, it may be
reused within the industrial facility for non-potable purposes like cooling
water or process water.
Monitoring and Compliance:
Continuous
monitoring and testing of effluent quality are crucial in ETPs to ensure
compliance with environmental regulations. Regular analysis helps in adjusting
treatment parameters and processes to maintain optimal performance.
Effluent
Treatment Plants are essential for industries to manage and mitigate the
environmental impact of their wastewater discharge. The design and operation of
an ETP depend on factors such as the type of industry, the characteristics of
the effluent, local regulations, and the desired quality of the treated water.
WELL WATER TREATMENT PLANT
A well water treatment plant is a facility or system designed to treat water extracted from wells, ensuring that it meets specific quality standards for safe consumption or use. Well water often contains impurities, contaminants, and minerals that may affect its safety, taste, and appearance. The treatment process varies depending on the characteristics of the well water and the desired water quality. Here are key components and processes commonly found in a well water treatment plant.
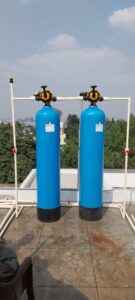
Water Intake:
Well water is drawn from underground aquifers through the well pump and enters the treatment plant.
Screening:
Initial screening removes large debris, such as sand, leaves, and twigs, from the well water to protect downstream equipment.
Pre-Chlorination:
Some well water treatment plants may use pre-chlorination to disinfect the water and control algae growth. Chlorine is added to kill bacteria and other microorganisms present in the well water.
Coagulation and Flocculation:
Chemicals, such as coagulants and flocculants, may be added to promote the aggregation of suspended particles, making them easier to remove in the subsequent sedimentation or filtration stages.
Sedimentation:
Sedimentation tanks allow heavier particles to settle to the bottom as sludge, leaving clearer water above. This is particularly effective for removing larger particles and some suspended solids.
Filtration:
Well water is passed through one or more filtration stages to remove remaining suspended particles, bacteria, and microorganisms. Common filtration methods include sand filtration, activated carbon filtration, and multimedia filtration.
Disinfection:
Disinfection is a crucial step to ensure that the treated well water is free from harmful microorganisms. Common disinfection methods include chlorination, ultraviolet (UV) irradiation, or ozonation.
PH Adjustment:
The pH of well water may be adjusted to meet drinking water standards. Chemicals such as lime or soda ash can be added to raise pH, while acids may be used to lower it.
Desalination (if applicable):
In regions where well water has high salinity, desalination methods such as reverse osmosis or distillation may be employed to remove dissolved salts and minerals.
Post-Chlorination:
After the treatment process, post-chlorination may be applied to maintain a residual disinfectant in the water distribution system, ensuring that the water remains microbiologically safe as it travels through pipelines.
Storage Tank:
Treated well water is often stored in a clean and sanitized storage tank before distribution to consumers. This helps maintain a consistent supply and pressure in the distribution system.
Distribution System:
The distribution system transports the treated well water to consumers’ homes, businesses, or other points of use. Pumps, pipelines, and storage reservoirs are part of this network.
Water Quality Monitoring:
Continuous monitoring of water quality parameters, such as turbidity, chlorine levels, pH, and microbial content, is essential to ensure that the treated well water meets regulatory standards.
Maintenance and Operations:
Regular maintenance, inspections, and adherence to operational protocols are crucial to the ongoing efficiency and reliability of the well water treatment plant.
Well water treatment plants are essential for providing safe and reliable drinking water to communities and industries that rely on well water sources. The design and components of such plants depend on the specific characteristics of the well water and the quality standards required for the intended use
IRON REMOVER PLANT
An iron remover plant, also known as an iron removal system or iron filtration system, is designed to treat water that contains elevated levels of iron and manganese. High concentrations of these elements in water can lead to issues such as discoloration, staining, and undesirable taste and odor. Iron remover plants use various methods to effectively reduce or eliminate iron and manganese from water. Here are key components and processes commonly found in an iron remover plant.
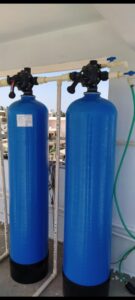
Water Intake:
The water containing elevated levels of iron and manganese is drawn into the iron remover plant from its source, such as a well or a municipal water supply.
Oxidation:
Iron and manganese often exist in water in a dissolved, ferrous state. The first step in many iron removal systems involves oxidation to convert these ferrous ions into ferric ions, which can be more easily filtered or settled. Common oxidizing agents include air, chlorine, or potassium permanganate.
Filtration:
The oxidized water is then passed through a filtration system to physically remove the solid particles of iron and manganese. Various types of filters may be used, such as sand filters, green sand filters, or multimedia filters. These filters trap the oxidized particles, preventing them from passing through.
Backwashing:
Periodically, the filter media needs to be cleaned to remove accumulated iron and manganese particles. This is achieved through a backwashing process where water flow is reversed through the filter, dislodging and flushing out the trapped particles.
Catalytic Media (Optional):
Some iron remover plants use catalytic filter media, such as manganese greensand or Birm, which enhance the oxidation and filtration processes. These media can effectively capture iron and manganese, promoting more efficient removal.
pH Adjustment (if needed):
Depending on the water’s pH level, it may be necessary to adjust it to an optimal range. pH adjustment can influence the efficiency of iron and manganese removal processes.
Post-Filtration Disinfection (if needed):
After filtration, the water may undergo additional disinfection processes to ensure that any remaining bacteria or microorganisms are eliminated. Common methods include chlorination or UV irradiation.
Monitoring and Control System:
An iron remover plant typically includes a monitoring and control system to track key parameters, such as iron and manganese levels, flow rates, and the status of filter media. This system helps optimize performance and ensures that treated water meets quality standards.
Residual Management:
Iron remover plants generate a waste stream during backwashing that contains concentrated iron and manganese particles. Proper management and disposal of this waste are essential to prevent environmental impact.
Water Storage and Distribution:
The treated water is stored in clean and sanitized storage tanks before being distributed to consumers through a network of pipelines. Adequate storage helps ensure a continuous and reliable water supply.
Regular Maintenance and Cleaning:
Regular maintenance, inspections, and cleaning of filter media are crucial to the ongoing efficiency of the iron remover plant. This includes periodic backwashing and, if necessary, media replacement.
Iron remover plants are commonly used in residential, commercial, and industrial settings where elevated iron and manganese levels in water pose aesthetic or operational challenges. The design and capacity of these plants depend on factors such as the water quality, flow rates, and the extent of iron and manganese contamination.